I enjoy the idea that a computer can have the capacity to feel and relay back those feelings, so I wanted to create a simple default, visual state for the computer. The default state is represented by a loop of three ellipses (like an ellipsis), and when this state is interrupted by the touch of a person the program responds with a very human-like response.

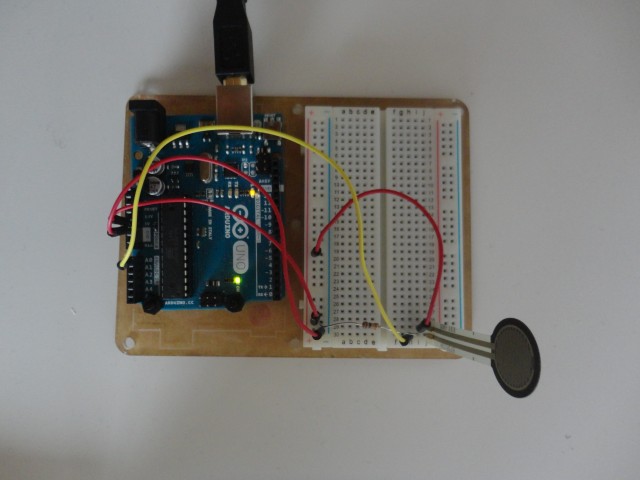
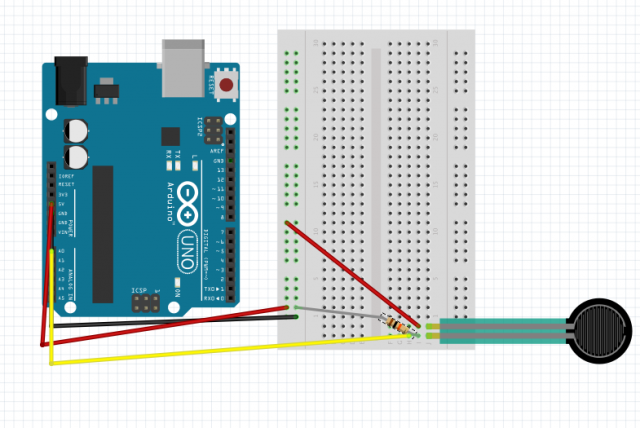
Processing Code:
import processing.serial.*;
Serial myPort;
int valueA; // Sensor Value A
int valueB; // Sensor Value B
int count = 2;
//------------------------------------
void setup() {
size(600, 200);
smooth ();
// List my available serial ports
int nPorts = Serial.list().length;
for (int i=0; i < nPorts; i++) {
println("Port " + i + ": " + Serial.list()[i]);
}
String portName = Serial.list()[2];
myPort = new Serial(this, portName, 9600);
serialChars = new ArrayList();
}
//------------------------------------
//------------------------------------
void draw() {
// Process the serial data. This acquires freshest values.
processSerial();
background (130);
// moment sensor is touched, text shows
if (valueA > 5) {
textSize (25);
fill (180);
text ("please stop, i don't feel like being touched", 50,45);
// this sets up ellipses to loop
}
else{
if(count<50){
noStroke ();
fill(240);
ellipse(250,100,20,20);
count++;
}
else if(count<100){
fill(240);
ellipse(250,100,20,20);
ellipse(300,100,20,20);
count++;
}
else if(count<150){
fill(240);
ellipse(250,100,20,20);
ellipse(300,100,20,20);
ellipse(350,100,20,20);
count++;
}
else if (count<175){
fill(130);
noStroke();
ellipse(250,100,20,20);
ellipse(300,100,20,20);
ellipse(350,100,20,20);
count++;
}
else{
count=2;
}
}
}
//---------------------------------------------------------------
ArrayList serialChars; // Temporary storage for received serial data
int whichValueToAccum = 0; // Which piece of data am I currently collecting?
boolean bJustBuilt = false; // Did I just finish collecting a datum?
void processSerial() {
while (myPort.available () > 0) {
char aChar = (char) myPort.read();
// You'll need to add a block like one of these
// if you want to add a 3rd sensor:
if (aChar == 'A') {
bJustBuilt = false;
whichValueToAccum = 0;
} else if (aChar == 'B') {
bJustBuilt = false;
whichValueToAccum = 1;
} else if (((aChar == 13) || (aChar == 10)) && (!bJustBuilt)) {
// If we just received a return or newline character, build the number:
int accum = 0;
int nChars = serialChars.size();
for (int i=0; i < nChars; i++) {
int n = (nChars - i) - 1;
int aDigit = ((Integer)(serialChars.get(i))).intValue();
accum += aDigit * (int)(pow(10, n));
}
// Set the global variable to the number we captured.
// You'll need to add another block like one of these
// if you want to add a 3rd sensor:
if (whichValueToAccum == 0) {
valueA = accum;
// println ("A = " + valueA);
} else if (whichValueToAccum == 1) {
valueB = accum;
// println ("B = " + valueB);
}
// Now clear the accumulator
serialChars.clear();
bJustBuilt = true;
} else if ((aChar >= 48) && (aChar < 57)) {
// If the char is between '0' and '9', save it.
int aDigit = (int)(aChar - '0');
serialChars.add(aDigit);
}
}
}
Arduino Code:
// This Arduino program reads two analog signals,
// such as from two potentiometers, and transmits
// the digitized values over serial communication.
int sensorValue0 = 0; // variable to store the value coming from the sensor
int sensorValue1 = 0; // variable to store the value coming from the other sensor
void setup() {
Serial.begin(9600); // initialize serial communications
}
void loop() {
// Read the value from the sensor(s):
sensorValue0 = analogRead (A0); // reads value from Analog input 0
sensorValue1 = analogRead (A1); // reads value from Analog input 1
Serial.print ("A");
Serial.println (sensorValue0);
Serial.print ("B");
Serial.println (sensorValue1);
delay (50); // wait a fraction of a second, to be polite
}